Дипломная работа: Проектирование привода общего назначения
Определим толщину фланцев поясов корпуса и крышки.
Толщину верхнего пояса корпуса и пояса крышки
определим по формуле (6.2):
(6.2)
где - см. формулу (6.1);
нижнего пояса корпуса по формуле (6.3):
(6.3)
где - см. формулу (6.1);
Принимаем
Определим диаметр болтов:
фундаментных по формуле (6.4):
(6.4)
где - см формулу (2.3);
принимаем болты с резьбой M 20;
крепящих крышку корпуса у подшипников по формуле (6.5):
(6.5)
где - см формулу (6.4);
принимаем болты с резьбой M 16;
соединяющих крышку с корпусом по формуле (6.6):
(6.6)
где - см формулу (6.4);
принимаем болты с резьбой M l2.
Компоновку обычно проводят в два этапа. Первый этап
служит для приближённого определения положения зубчатых колес, для последующего
определения опорных реакций и подбора подшипников.
Компоновочный чертёж выполняем в одной проекции разрез
по осям валов при снятой крышке редуктора.
Примерно по середине листа параллельно его длинной
стороне проводим горизонтальную осевую линию; затем две вертикальные линии - оси
валов на расстоянии 
Вычерчиваем упрощённо шестерню и колесо в виде
прямоугольников; шестерню выполняем за одно целое с валом; длина ступицы колеса
равна ширине венца и не выступает за пределы прямоугольника.
Очерчиваем внутреннюю стенку корпуса:
а). принимаем зазор между торцом шестерни и внутренней
стенкой корпуса

б). принимаем зазор от окружности вершин зубьев колеса
до внутренней стенки корпуса

в). принимаем расстояние между наружным кольцом
подшипника ведущего вала и внутренней стенкой корпуса 
Так как диаметр вершин зубьев шестерни ведущего вала
равен 126,37мм, по конструктивным соображениям для удобства монтажа намечаем
роликоподшипники конические однорядные средней широкой серии, где диаметр
подшипников равен 120мм. Для ведомого вала намечаем радиальные подшипники
тяжелой серии. Габариты подшипников выбираем по диаметру вала в месте посадки
подшипников и
. Параметры
подшипников определяем в соответствии с таблицей приложения 7 [1] и сводим в
таблицу 2.
Таблица 2 - Параметры подшипников.
Условное обозначение подшипника |
Размеры подшипников, мм |
Грузоподъёмность, кН |
d |
D |
B |
C |
Co |
7611 |
55 |
120 |
45,5 |
160,0 |
140,0 |
7614 |
70 |
150 |
51 |
240,0 |
186 |
Решаем вопрос о смазывании подшипников. Принимаем для
подшипников пластичный смазочный материал. Для предотвращения вытекания смазочного
материала внутрь корпуса
вымывания пластичного смазочного материала жидким
маслом из зоны зацепления устанавливаем мазеудерживающие кольца. Их ширину
определяет размер 
Измерением находим расстояние между опорами на ведущем
валу и на
ведомом ; принимаем
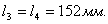
Глубина гнезда подшипника 7611: ; для подшипника 7614;
Толщину фланца крышки подшипника
принимают примерно равной диаметру отверстия  . Высоту головки болта примем 
Предварительная компоновка редуктора представлена на
рисунке 3.
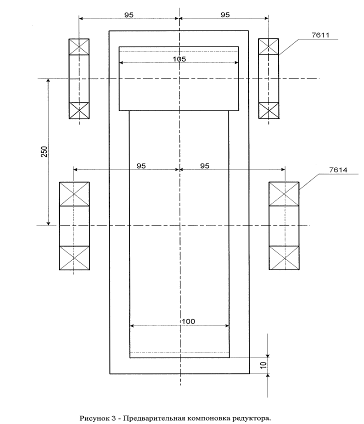
Выбираем приводную роликовую однорядную цепь. Вращающий
момент на ведущей звездочке: Передаточное число цепной
передачи Определим
число зубьев:
ведущей звездочки по формуле (8.1):
(8.1)
принимаем 
ведомой звездочки по формуле (8.2):
(8.2)
принимаем
Тогда фактическое передаточное число равно:

Отклонение составит: что меньше допустимого, равного
3%.
Расчетный коэффициент нагрузки определим по формуле (8.3):
(8.3)
где - динамический коэффициент, в
соответствии с рекомендацией на с.149 [1] при
спокойной нагрузке (передача к ленточному конвейеру)
- коэффициент, учитывающий
влияние межосевого расстояния, в соответствии с
рекомендацией на с.150 [1]
- коэффициент, учитывающий
влияние угла наклона линии центров (в данном случае
угол не превышает 60°), в соответствии с рекомендацией
на с.150 [1]
- коэффициент, учитывающий способ
регулирования натяжения цепи, в соответствии с рекомендацией на с.150 [1] при
периодическом регулировании
- коэффициент, при непрерывной смазке цепи в соответствии с рекомендацией
на с.
150 [1]
- коэффициент при двусменной работе в соответствии с рекомендацией на с.150
[1]

Для определения шага цепи ориентировочно зададимся
величиной допускаемого давления в шарнирах опоры. Ведущая звездочка имеет
частоту вращения
Среднее значение допускаемого давления в соответствии
с рекомендациями в таблице 7.18 [1] Определим шаг однорядной цепи по
формуле (8.4):
(8.4)
где - вращающий момент на ведомом
валу, ;
- число зубьев ведущей звездочки,
- расчетный коэффициент нагрузки, по расчету 
Подбираем в соответствии с таблицей 7.15 [1] цепь
ПР-50,8-226,8 в соответствии с ГОСТ 13568-75, имеющую шаг цепи разрушающую нагрузку массу проекцию
опорной поверхности шарнира
Определим скорость цепи по формуле (8.5):
(8.5)
где - число зубьев ведущей звездочки,
п2 - частота
вращения ведущей звездочки, 
t - шаг
цепи,
Окружную силу определим по формуле (8.6):
(8.6)
где - вращающий момент на ведомом
валу, 
- угловая скорость ведомого вала, 
- см. формулу (8.5).
Давление в шарнире проверим по формуле (8.7):
(8.7)
где - см. формулу (8.6);
- см. формулу (8.3);
- проекция опорной поверхности
шарнира, = 473мм.
Уточняем по таблице 7.18. [1] допускаемое давление:

где р - табличное значение допускаемого давления по
таблице 7.18 при и

- число зубьев ведущей звездочки,
следовательно, условие p< выполнено.
Число звеньев цепи определим по формуле (8.8):
(8.8)
где 
;
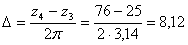
Округляем до четного числа = 152.
Уточняем межосевое расстояние для цепной передачи по
формуле (8.9):
(8.9)
где t - шаг цепи, t=44.45мм;
- число звеньев цепи, =152;
- суммарное количество зубьев
ведущей и ведомой звездочек, =101;
- см. формулу (8.8).
Для свободного провисания цепи предусматриваем
возможность уменьшения межосевого расстояния на 0,4%, т.е. на .
Определим диаметры делительных окружностей звездочек
по формулам (8.10), (8.11):
(8.10)
(8.11)
Определим диаметры наружных окружностей звездочек по
формулам (8.12), (8.13):
(8.12)
(8.13)
где - диаметр ролика цепи, в
соответствии с таблицей 7.15 [1]
Определим силы, действующие на цепь:
окружная сила определена выше: 
от центробежных сил определим по формуле (8.14):
(8.14)
где q - масса цепи, q=7,5кг/м;
v - скорость
цепи,
от провисания по формуле (8.15):
(8.15)
где - коэффициент, учитывающий
расположение цепи, при горизонтальном положении цепи
q - масса цепи, 
- межосевое расстояние, .
Расчетную нагрузку на валы определим по формуле (8.16):
(8.16)
Проверим коэффициент запаса прочности цепи по формуле
(8.17):
(8.17)
где Q - разрушающая
нагрузка см. таблицу 7.15 ,
- окружная сила, = 5747Н;
- динамический коэффициент, в соответствии с рекомендацией на с.149 [1] при
спокойной нагрузке (передача к ленточному конвейеру) = 1;
Fv - действующая на цепь от центробежных сил, Fv =35Н;
Ff - сила, действующая на цепь от провисания цепи, Ff =1072Н.
Это больше, чем нормативный коэффициент запаса в
соответствии таблицей 7. 19 [1] равный
следовательно, условие прочности
выполнено.
Определим размеры ведущей звездочки:
диаметр ступицы звездочки определим по формуле (8.18):
(8.18)
где - диаметр выходного конца
ведомого вала, =65мм.
Страницы: 1, 2, 3, 4, 5
|