Курсовая работа: Проектування технологічного оснащення для оброблення деталі "Кронштейн 6464.4700.015"
=1,5; =1,0; =1,15; =1,0; =1,2; =1,0, =1,5.

При обробленні
площини необхідно забезпечити дотримання двох умов:
заготовка не
повинна переміщуватися (зсуватися) під дією колової складової зусилля різання ;
заготовка не
повинна провертатися відносно вісі під
дією момента різання .
Розрахункова
схема для визначення необхідної сили затиску зображена
на рис..
На розрахунковій
схемі прийнято такі позначення:
– момент різання, Н×м; – колова складова
сили різання, Н; – сила
затиску, Н; – реакція опори, Н;
– cила тертя у точці
прикладання сила затиску , Н;
– cила тертя у точці
прикладання реакції опори , Н.
Із геометричних
побудов приймаємо м; м; м; м; м; м; м; м.
Для спрощення
розрахунків приймаємо, що реакції опор і повнопрофільного пальця однакові.
Запишемо рівняння
рівноваги для визначення сили затиску :
(1.7.1)
, (1.7.2)
, (1.7.3)
, (1.7.4)
де , , - коефіцієнти тертя.
Із врахуванням (1.7.2), (1.7.3), (1.7.4) рівняння (1.7.5) матимуть вигляд:
(1.7.5)
Маємо два
рівняння рівноваги та два невідомих , – cтатично визначена
задача.
Рис.1.7.1. Розрахункова схема для визначення
необхідної сили затиску
Момент різання та колову складову
сили різання визначають за емпіричними
залежностями:
колова складова
сили різання 
(1.7.6)
Сp=54,5, х=0,9;
y=0,74; u=1,0; q=1,0; w=0 - табл. 41, стор. 291, [4]; SZ=0,08
мм/зуб - табл. 33, стор. 285, [4]; kMp=1,0; t=1,0
мм; B=128 мм; z=10; D=160 мм; n=125 хв-1.
Н.
момент різання :
(1.7.7)
Н×м.
Прийнявши - табл. 10, стор. 85, [4],
спрощуємо рівняння і розв’язуємо спрощену систему рівнянь (2.19) в середовищі Mathcad.
(1.7.8)
Розв’язок
систем рівнянь в середовищі Mathcad
Отже, сила
затиску для нашого випадку становить Q=4916,4 Н.
Сумарну силу затиску
при закріпленні однієї заготовкизнайдемо згідно рис. 1.7.2 за правилом трикутника:
Рис. 2.4.
Розрахункова схема для визначення сумрного зусилля затиску при закріпленні
однієї заготовки
(1.7.9)
Н.
В якості приводу
приймаємо два пневмоциліндри, які живляться від пневмомережі підприємства.
Зусилля на штоці кожного пневмоциліндра при використанні пристрою важільного
типу
,
Звідси, ,
Для зменшення
зусилля приводу приймаємо
.
Н.
Рис. 1.7.3 Розрахункова схема для визначення
зусилля приводу
Діаметр поршня
пневмоциліндра визначають за формулою:
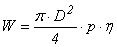
де – тиск повітря в
пневмомережі, приймаємо МПа;
- коефіцієнт корисної дії
пневмоциліндра; приймаємо .
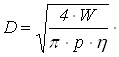
мм.
Приймаємо мм.
В зв’язку із
малою величиною ходу штока вибираємо конструктивне виконання пневмоциліндра –
вбудований у конструкцію верстатного пристрою.
Така конструкція
пневмоциліндра передбачає меншу величину ходу штока у порівнянні із
стаціонарним поршневим пневмоциліндром.
Приймаємо
конструктивні та технологічні параметри вбудованого пневмоциліндра:
робочий тиск - МПа;
діаметр поршня
пневмоциліндра - мм;
діаметр штока - мм.
1.8
Спеціальні види розрахунків
Розрахунок
елементів пристрою на міцність
Розрахуємо
мінімальний діаметр опори важеля,
що здійснює затиск заготовки у пристрої.
Із умови міцності
на зминання можна записати:
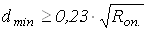
де - діаметр опори важеля,
мм; - реакція опори
важеля, Н.
Реакцію опори
важеля визначаємо

Н.
мм.
Приймаємо мм.
1.9 Економічне обґрунтування
ефективності використання пристрою
Для визначення
економічної ефективності порівнюємо два значення технологічної собівартості
оброблення заготовки на даній операції при використанні старого Сс
та нового Сн пристроїв:
, (1.9.1)
, (1.9.2)
де Зс,
Зн – основна заробітна плата при виконанні даної операції;
z -цехові накладні витрати
(приймаємо рівними 300 %);
qп - коефіцієнт проектування
заданого пристрою (приймаємо рівним 0,5);
qе
– коефіцієнт
експлуатації пристрою (витрати на експлуатацію) (приймаємо рівним 0,3);
і – термін служби пристрою
(приймаємо рівним 3 роки);
N – річна програма випуску
деталей, штук;
Sc,
Sн
- собівартість виготовлення відповідно старого та нового пристроїв.
Основну заробітну
плату можна визначити таким чином:
, (1.9.3)
де tшт.-
штучний час оброблення на відповідному переході, хв;
- погодинна тарифна ставка
робітника першого розряду; =4,447
грн./год;
m – тарифний
коефіцієнт. Тоді
(1.9.4)
(1.9.5)
Приймаємо , .
Штучну норму часу
визначаємо укрупнено. Вважаємо, що старий пристрій проектувався для умов
дрібносерійного виробництва із обробленням однієї заготовки на
горизонтально-фрезерному верстаті. Тоді
, (1.9.6)
, (1.9.7)
де , основний час оброблення
відповідних поверхонь при використанні старого та нового пристрою;
, -
коефіцієнти пропорційності між основним та штучним часами; приймаємо , - дод. 3, стор.259, [6].
Основні часи , визначають на основі
емпіричних залежностей дод. 2, стор.249, [6]:
, (1.9.8)
, (1.9.9)
де - шлях різання при
обробленні площини.
хв.
хв. Тоді
хв.
хв. Звідси,
грн.
грн.
Собівартість
виготовлення пристрою в залежності від його складності можна визначити за
формулою:
, (1.9.10)
(1.9.11)
(1.9.12)
де n –
кількість основних деталей у пристрої; приймаємо 22;
30. Спит. - питома собівартість
пристрою на одну деталь; приймаємо грн; грн.
грн.
грн.
Визначаємо
технологічну собівартість оброблення заготовки на даній операції при
використанні старого Сс та нового Сн пристроїв:
грн.
грн.
Економічний ефект
від використання нового пристрою в розрахунку на річну програму випуску, грн:
(1.9.13)
грн.
Термін окупності
пристрою (в роках) визначають за формулою:
, (1.9.14)
де q –
видатки, пов’язані з експлуатацією пристрою(ремонт, обслуговування та
налагодження), у % від вартості пристрою; приймаємо q=35 %.
року » 5,6 місяців.
1.10 Опис конструкції та роботи
пристрою
Креслення даного
пристрою приведено у графічній частині курсового проекту (ДП. ПТСТС.
083100.000.СК).
У корпусі 3
пристрою для фрезерування поверхонь в розмір 15h14-0,43 мм закріплено
два пневмоциліндри 1, які закриті кришками 2 із ущільненнями 22 за допомогою
гвинтів 18 із шестигранними заглибленнями під ключ. Корпус базується на столі
горизонтально-фрезерного верстату за допомогою двох напрямних шпонок 26, що
з’єднані із корпусом гвинтами 15 із шестигранним заглибленням під ключ. До
корпуса 3 зверху приєднана плита 4, яка фіксується чотирнадцятьма гвинтами 16.
Кожна із двох оброблюваних деталей (зображено умовно) базується на
повнопрофільний палець 19 та три опорні пальці 20, причому палець 19 та два з
трьох пальців 20 з’єднані відповідними посадками із плитою 4, а третій палець
20 закріплений у стійці 5. Кожна із стійок 5 приєднана до плити 4 гвинтами 17
та штифтами 27. До задньої стінки корпусу 3 за допомогою різевих з’єднань
приєднані дві вилки 7 , на яких на вісях 9 закріплено два коромисла 6. До
верхнього кінця кожного із коромисел 6 за допомогою вісі 10 приєднано призму
21. Від осьового переміщення коромисел 6 і призм 21 обмежують гайки 14 та шайби
25. Нижніми кінцями коромисла 6 приєднані до вушок 8 за допомогою вісей 11 із
гайками 13 та шайбами 24. У свою чергу вушка 8 за допомогою різевих з’єднань
приєднані до штоків пневмоцилідрів 1 та фіксуються гайками 14. Для напрямлення
штоків пневмоциліндрів 1 під час роботи та запобіганню їх передчасному
зношуванню служать закріплені у корпусі 3 втулки 12. Для транспортування
верстатного пристрою служать два рим-болти 23 У корпусі 3 передбачено місця для
приєднання штуцерів трубопроводів пневмосистеми.
Пристрій для
фрезерування поверхонь в розмір 15h14-0,43 мм
працює таким чином. Дві оброблювані заготовки базуються за допомогою двох
повнопрофільних пальців 19 і шістьох опорних пальців 20. Після цього вмикають
пневмосистему, і повітря по трубопроводах поступає у праві порожнини
пневмоциліндрів, внаслідок чого їх поршні починають переміщуватися вліво. За
рахунок переміщення поршнів пневмоциліндрів 1 починають рухатися штоки із
вушками 8, які через вісі 11 діють на нижні кінці коромисел 6. Коромисла 6,
повертаючись на вісях 9 у вилках 7, здійснюють затиск заготовок за допомогою
призм 21. Розкріплення та зняття заготовки відбувається у зворотній
послідовності: повітря подають у ліві порожнини пневмоциліндрів, поршні
здійснюють переміщення вправо, що спричиняє переміщення штоків із вушками 8;
рух штоків із вушками 8викликає провертання коромисел 6 на вісях 9 у
протилежний бік, і заготовки розкріплюються.
2.
2.1 Розроблення пристрою для
контролю перпендикулярності поверхні 3 відносно отвору 6 (база Б) (згідно
креслення деталі - “Кронштейн 6464.4700.015”)
2.1.1 Аналіз конструкцій контрольного
пристрою та вибір раціоанльної
У практиці роботи
машинобудівних підприємств виникає необхідність контролю перпендикулярності
торців, радіального й торцьового биття деталей машин відносно центральних
отворів. Такі перевірки в переважній більшості виконують на контрольних
оправках, які встановлюють у центрових бабках з індикаторами на стійках.
Дані універсальні
методи контролю мають загальний недолік: вони вимагають виконання значної
кількості трудомістких ручних операцій, пов’язаних із значними витратами часу й
фізичних сил контролера.
Тому отримали
поширення спеціальні контрольні пристрої, в яких оправка встановлена в корпусі
пристрою, а надіваються і знімаються лише деталі, що підлягають контролю, або
оправку встановлюють в деталь, що лежить на столі, де і відбувається перевірка.
Вимірні вузли є складовими частинами пристрою і закріплені або на корпусі, або
на оправці.
У той же час на
фінішних, викінчувальних і контрольних операціях технологічних процесів
механічного оброблення деталей машин широко використовують самоцентрівні
пристрої з гідро-пластмасою. Центрування та затиск деталей у цих пристроях
здійснюють по внутрішній або зовнішній поверхні за допомогою тонкостінної
оболонки, яка розтискається при центруванні по внутрішній поверхні або
стискається при центруванні по зовнішній поверхні за допомогою гідро-пластмаси.
Страницы: 1, 2, 3, 4
|