Курсовая работа: Редуктор цилиндрический
г) изгибающий момент
под муфтой в обеих плоскостях: 
5. Определяем
расчетный диаметр вала под подшипником С. Для этого сечения имеем:
Мгор = 0Н·м; Мвер = 162Н·м;
Т2=164Н·м;
следовательно ;
.
Тогда
.
По ГОСТ 6636-69
принимаем dC = 40мм.
Под подшипником D
принимаем такой же диаметр, т.е. dC = dD = dп=40мм.
6. Определяем
расчетный диаметр вала под колесом. Для этого сечения имеем:
Мгор = 33Н·м; Мвер = 69Н·м;
Т2=164Н·м;
следовательно ;
.
Тогда
.
С учетом ослабление
вала шпоночной канавкой, увеличиваем диаметр вала на 10℅. Таким образом, .
Полученный диаметр округляем по ГОСТ 6636-69
с таким расчетом, чтобы диаметр под колесом
, т.е. 37+2 39мм,
по ГОСТ 6636-69
принимаем = 42мм.
7. Диаметр вала под
муфту определен [см. п. 5] dм = 35
мм.
Таким образом, для
данного вала имеем диаметры: dC= dD= dп = 40мм, dK=42мм,
dМ = 35мм.
6.4. Расчет вала на
выносливость
Примем, что нормальные
напряжения осей изгиба изменяется по симметричному циклу, а касательные осей
кручения – по пульсирующему циклу. Определим коэффициент запаса прочности для
опасного сечения вала и сравним с допускаемым значением запаса. Прочность
соблюдается при
S > [S] = 1,5…2,0.
Коэффициенты запаса
определяются по формулам:
,
где - коэффициенты запаса
соответственно по нормальным и касательным напряжениям. Они определяются по
формулам:
; ,
где - пределы выносливости
материала вала; - амплитуда и
среднее напряжение циклов нормальных и касательных напряжений. Для
симметричного цикла нормальных напряжений =
0; - эффективные коэффициенты
концентрации напряжений; -
масштабные факторы; - коэффициенты
качества поверхности, принимаем равным единице; -
коэффициенты, учитывающие влияние асимметрии цикла.
Проверим на
выносливость ведомый (тихоходный) вал, так как крутящий момент этого вала
наибольший.
Материал вала – сталь
45, нормализация = 570МПа; = 246МПа;
= 142МПа.
Рассмотрим сечение под
подшипникам на него действуют изгибающие и крутящие моменты. Концентрация
напряжений вызвана напрессовкой подшипника.
Суммарный изгибающий
момент:
.
Моменты сопротивления
изгибу и кручению:
;
.
Коэффициенты понижения
пределов выносливости:

= 1 (шлифование); .
Амплитуда нормальных
напряжений:
.
Амплитуда и среднее
напряжение цикла касательных напряжений:
.
Определяем
коэффициенты запаса прочности:
;
;
.
В рассматриваемом
случае условие S > [S] = 1,5…2,0 выполняется.
7. Выбор и расчет
подшипников
7.1. Выбор
подшипников быстроходного вала
Исходные данные: радиальные нагрузки на подшипники FrA=260Н, FrB=2145Н; внешняя осевая нагрузка Fa1= 0H; частота вращения вала п1=735об/мин;
диаметр вала под подшипниками dn=25мм; расстояние между подшипниками l=104мм;
требуемый ресурс подшипников [Lh]=15000 ч; режим работы
– умеренные толчки; температура подшипникового узла t<100˚С.
1. На подшипники
действуют радиальные усилия, поэтому назначаем радиальные однорядные шарикоподшипники
по ГОСТ 8338-75 как наиболее распространенный тип подшипников для передачи с цилиндрическими
зубчатыми колесами.
2. Выбираем схему
установки подшипников.
Схема установки радиально
подшипников (в распор, в растяжку, со сдвоенной опорой) назначается в
зависимости от вида подшипников (шариковые или роликовые), его внутреннего
диаметра dn и расстояния между подшипниками l.
В нашем случае при dn=25мм
и l=104мм принимаем схему установки подшипников «в
распорку», для шарикоподшипников
.
3. Назначаем
типоразмер подшипника. Исходя из того, что диаметр вала под подшипник равен dn=25мм,
назначаем шарикоподшипник легкой серии: типоразмер 205, имеющий dn=25мм,
D = 52 мм, динамическую грузоподъемность С
= 14кН, статическую грузоподъемность С0 = 7кН.
4. Определяем основные составляющие радиальных
нагрузок на подшипники.
Для шарикоподшипников
,
где определяется по таблице (в
нашем случае, для подшипника 205 имеем е = 0,19); - радиальная нагрузка на
подшипник.
В нашем случае
;
.
Находим значения
осевых нагрузок.
В нашем случае
,
следовательно,
;
.
5. Определяем
эквивалентную динамическую нагрузку FЭ. При переменном режиме нагружения, заданном графиком
(см. задание), для подшипников редуктора имеем
,
где коэффициент
долговечности
.
В нашем случае
коэффициент долговечности
.
Номинальная
эквивалентная нагрузка определяется по
зависимости
.
Здесь - кинематический
коэффициент, учитывающий снижение долговечности при неподвижном внутреннем
кольце подшипника = 1.
Коэффициент
безопасности , определяем по
рекомендации [4 стр. 339] в зависимости от характера работы. При нагрузке с
умеренными толчками принимаем = 1,4.
Температурный
коэффициент , вводимый при температуре
подшипникового узла t<100˚C,
температурный коэффициент = 1 при t<100˚C.
и -
радиальная и осевая нагрузки на подшипники, возникающие при действии
номинального момента Tном.
X,Y – коэффициенты радиальной и осевой нагрузки,
назначаемые для конических роликоподшипников по ГОСТ 18855-82 в зависимости от
отношения .
В нашем случае для
подшипника I (подшипник А) имеем
.
Тогда XI = 1; YI = 0 (был принят
ранее по каталогу).
Для подшипника II
(подшипник В) аналогично
Таким образом,
.
.
Так как наиболее
нагруженным оказался подшипник II (опора В), то все
дальнейшие расчеты будим производить для этого подшипника.
6. Рассчитаем
долговечность назначенного подшипника 208 В
.
Для шарикоподшипников
принимают р = 3.
Коэффициент,
учитывающий совместное влияние качества метала и условие эксплуатации (смазка,
перекос подшипника),а23=0,75 зависит от типа подшипника и
расчетных усилий.
Коэффициент а1
=1, зависит от уровня надежности Р (вероятности безотказной работы).
7.2. Выбор
подшипников тихоходного вала
Исходные данные: радиальные нагрузки на подшипники FrС= 3255Н,
FrD=1514Н; частота вращения вала п2=215об/мин;
диаметр вала под подшипниками dn=40мм; расстояние между подшипниками l=101мм;
требуемый ресурс подшипников [Lh]=15000 ч; режим работы
– умеренные толчки; температура подшипникового узла t<100˚С.
1. На подшипники
действуют радиальные усилия, поэтому назначаем однорядные радиальные шарикоподшипники
по ГОСТ 8338-75 как наиболее распространенный тип подшипников для передачи с цилиндрическими
зубчатыми колесами.
2. Выбираем схему
установки подшипников.
Схема установки
радиальных подшипников (в распор, в растяжку, со сдвоенной опорой) назначается
в зависимости от вида подшипников (шариковые или роликовые), его внутреннего
диаметра dn и расстояния между подшипниками l.
В нашем случае при dn=40мм
и l=101мм принимаем схему установки подшипников «в
распор», для шарикоподшипников
.
3. Назначаем
типоразмер подшипника. Исходя из того, что диаметр вала под подшипник равен dn=40мм,
назначаем шарикоподшипник легкой серии: типоразмер 208, имеющий dn=40мм,
D = 80 мм, динамическую грузоподъемность С
= 25,2кН, статическую грузоподъемность С0 = 17,8кН.
4. Определяем основные составляющие радиальных
нагрузок на подшипники.
Для шарикоподшипников
,
где определяется по таблице (в
нашем случае, для подшипника 208 имеем е = 0,19); - радиальная нагрузка на
подшипник.
В нашем случае
;
.
Находим значения
осевых нагрузок .
В нашем случае
,
следовательно,
;
.
5. Определяем
эквивалентную динамическую нагрузку FЭ. При переменном режиме нагружения, заданном графиком
(см. задание), для подшипников редуктора имеем
,
Где выбор номинальной
эквивалентной нагрузки и где
коэффициента долговечности был
описан ранее
Таким образом,
.
.
Так как наиболее
нагруженным оказался подшипник I (опора С), то все
дальнейшие расчеты будим производить для этого подшипника.
6. Рассчитаем
долговечность назначенного подшипника 208 С
.
Для шарикоподшипников
принимают р = 3.
Коэффициент,
учитывающий совместное влияние качества метала и условие эксплуатации (смазка,
перекос подшипника),а23 зависит от типа подшипника и
расчетных усилий.
Коэффициент а1
зависит от уровня надежности Р (вероятности безотказной работы).
8. Выбор шпонок
Шпонки призматические
со скругленными торцами. Размеры сечений шпонок, пазов и длины шпонок
определяем по ГОСТ 23360-78. материал шпонок – сталь 45 нормализация.
Определим напряжение
смятия и условие прочности по формуле:
,
где Т –
вращающий момент, передаваемый шпонкой; d – диаметр
вала на котором установлена шпонка; b, h,
l – соответственно ширина, высота и длина шпонки; t1 – глубина паза вала под
шпонку.
[σсм] = 100…120МПа – допускаемое напряжение смятия
при стальной ступице. [σсм] = 50…70МПа
– допускаемое напряжение смятия при чугунной ступице.
Ведущий (быстроходный)
вал
Из двух шпонок – под
шестерней и под шкивом.
-
шпонка под шестерней:
d = 25мм; b
x h = 8 x 7; t1 = 4мм; l = 56мм (при длине ступицы
шестерни 60мм):
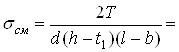 .
-
шпонка под шкивом:
d = 20мм; b
x h = 6 x 6; t1 =3,5мм; l = 56мм
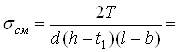 .
Ведомый
(тихоходный) вал.
Из двух шпонок – под
зубчатом колесом и под муфтой – более нагружена вторая (меньше диаметр вала и
поэтому меньше размеры поперечного сечения шпонки). Поверим шпонку под муфтой: d
= 35мм;
b x h
= 10 x 8; t1 = 5мм; l = 90мм
(при длине ступицы муфты 96мм); момент Т2 = 164Н·м:
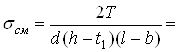 .
Условие σсм
< [σсм] выполняется во всех рассматриваемых случаях.
9. Выбор смазки,
зацепления подшипников
Экономичность и
долговечность машины в большой степени зависит от правильности выбора
смазочного материала. Обычно значения коэффициентов трения в парах трения
снижается с ростом вязкости смазочного материала, но вместе с тем повышаются
гидромеханические потери на перемешивание смазочного материала.
Для смазывания
зубчатых передач со стальными зубьями ориентировочное значение вязкости масла
определяется по рис. 19.1 (заштрихованная зона) в зависимости от фактора [2 стр. 346]:
,
где - твердость по Виккерсу
активных поверхностей зубьев ( =286); - контактные напряжения, МПа
( = 476МПа); - окружная скорость в
зацеплении, м/с ( = 2,8м/с).
Следовательно:
Из рекомендуемого
диапазона значений вязкости выбирают величину, наиболее соответствующую
конкретным условиям. Верхний предел рекомендуется назначать при зубчатых
колесах из стали одной марки или, если хотя бы одно из них выполнено из
никелевой или хромоникелевой стали.
При = 231, вязкость масла . По таблице 19.1
[2 стр. 345]
определяем марку масла: при вязкости соответствует
индустриальному маслу (ГОСТ 20799-75) И-100А.
Объем данного масла
необходимого для нормальной работы равен
V= 2 л.
При смазывании
погружением конических зубчатых колес уровень масла в ванне должен обеспечивать
смачивание зубьев одного из колес по всей длине зуба.
Подшипники смазываем
пластичным смазочным материалом, закладываем в подшипниковые пары при монтаже.
Сорт смазки выбираем по таблице 19.2 [2 стр. 345] – солидол жировой УС-2 ГОСТ
1033-79.
Список
использованной литературы
1.
Иванов М.Н. Детали машин. – М.:
Высш. шк., 1984. – 336 с.
2.
Курсовое проектирование деталей
машин/В.Н. Кудрявцев, Ю.А. Державиц, И.К. Арефьев и др. – Л.: Машиностроение,
1984. – 400 с.
3.
Дунаев П.Ф. Конструирование узлов
и деталей машин: Учеб. пособие для вузов. – 3-е изд., перераб. и доп. – М.:
Высш. школа, 1978. – 352 с.
4.
Чернин И.М., Кузьмин А.В., Ицкович
Г.М. Расчеты деталей машин. – Минск: Вышэйшая школа, 1978. – 472 с.
5.
Детали машин. Атлас конструкций.
Кол. Авторов по ред. д-ра техн. Наук Д.Н. Решетова. Изд. 3-е переработ. и доп.
М., изд-во «Машиностроение», 1970, 360 стр.
6.
Решетов Д.Н. Детали машин. – М.:
Машиностроение, 1989. – 496 с.
|