Курсовая работа: Технология ремонта автосцепки СА-3
Правку выполняют с предварительным
нагревом до температуры 800 – 850°C с выдержкой в печи не менее 1 часа для
равномерного прогрева корпуса. Заканчивать правку необходимо при температуре
выправляемых зон не менее 650°C для предотвращения образования термических
трещин.
Правку производят на специализированных
гидравлических прессах. При устранении уширения зева в корпус вставляют
ограничитель, исключающий сужение зева больше нормы.
Охлаждение корпусов
производят в помещениях при отсутствии сквозняков, не применяя воду или другую
охлаждающую среду.
Трещины и износы,
выявленные в корпусе автосцепки, ремонтируют сваркой и наплавкой. Разрешается
при всех видах ремонта вагонов:
- заваривать вертикальные
трещины сверху и снизу в углах зева, если они не выходят за положение верхнего
или нижнего зуба;
- заваривать трещины в
углах окон для замка и замкодержателя, если после разделки трещины в верхней
части не выходят на горизонтальную поверхность головы и за положение верхнего
ребра со стороны большого зуба, а в нижней части имеют длину не более 20 мм;
- вырубать трещины
глубиной до 5 мм в хвостовике корпуса с плавным переходом на поверхность без
заварки. Трещины перемычки глубиной не более 8 мм можно заваривать при условии,
что после их разделки толщина перемычки будет не менее 40 мм;
- заваривать трещину
перемычки между отверстиями для направляющего зуба и сигнального отростка
замка, если трещина не выходит на вертикальную стенку корпуса;
- заваривать трещину хвостовика
автосцепки. Общая длина ремонтируемых трещин хвостовика в зоне от упора до
передней кромки отверстия для клина не более 100 мм у корпусов, проработавших
свыше 20 лет и более 150 мм для остальных корпусов;
- наплавлять изношенные
поверхности 6 контура зацепления так чтобы сварочные швы не доходили до мест
закруглений ближе 15 мм.
Переход от
отремонтированной наплавкой ударной поверхности стенок зева к неизношенной
должен быть плавным, по длине не менее 15 мм. Твердость наплавленного металла
ударно-тяговых поверхностей должна быть не менее 250 НВ для грузовых вагонов и
не менее 450 НВ для пассажирских и рефрижераторных. Для обеспечения необходимой
твердости наплавку следует выполнять электродами ОЗН-400, порошковой проволокой
ПП-ТН350, ПП-ТН500 или пластичными электродами с использованием легирующих
присадок.
Разрешается при всех
видах ремонта:
- наплавлять
поверхности корпуса, соприкасающиеся при работе с центрирующей болочкой,
тяговым хомутом, ударной розеткой и клином тягового хомута при износе более 3
мм, но не более 8 мм;
- наплавлять изношенную
полочку предохранителя и шип для замкодержателя или приваривать новые в случае
их излома;
- наплавлять оба
изношенных отверстия для валика подъемника;
- наплавлять места
опоры стенки замкодержателя на корпус, нижней перемычки в окне для замка и
задней наклонной части дна карманов;
- наплавлять изношенный
торец хвостовика, если его длина менее 645 мм для автосцепки СА-3 и менее 654
мм для автосцепки СА-3М;
- наплавлять изношенную
перемычку хвостовика, если ее толщина в средней части не менее 40мм – для СА-3М.
Разделка кромок трещин производится
с применением ручного или пневматического зубила, электродуговой или
газокислородной резкой. При ремонте трещин в зеве необходим подогрев головы
автосцепки до температуры 250 – 300°C, что улучшает качество наплавленного
металла и снижает термические напряжения.
Ограничители
вертикальных перемещений вагонов не должны иметь изгибов и износов более 5 мм. Автосцепки
вагонов для перевозки опасных грузов оборудованы как нижними, так и верхним
ограничителями.
В деталях механизма
автосцепки при всех видах ремонта вагонов разрешается:
У замка наплавка изношенной
поверхности замыкающей части , овального отверстия при износе не более 8 мм,
направляющего зуба , поверхности радиальной опоры, шипа для предохранителя. В
случае излома шипа или сигнального отростка допускается их приварка. Твердость направленного
металла замыкающей части замка должна быть не менее 250 НВ, а для пассажирских
и рефрижераторных вагонов – не менее 400 – 450 НВ. Замыкающие части замков
рекомендуется упрочнять контактно -дуговой сваркой, что значительно повышает их
износостойкость. Упрочнение замка происходит в результате воздействия электрической
дуги и переноса на замыкающую часть материала электрода, в качестве которого
используют роликовые подшипники из стали ШХ-15СГ;
У замкодержателя
заваривать не более одной трещины; наплавлять изношенные поверхности
противовеса , отверстия , лапы , расцепного угла ; править погнутые детали в нагретом
состоянии до температуры 820 – 900°C;
В предохранителе замка наплавлять
износы верхнего плеча и отверстия под шип замка , править изгибы плеч в
нагретом состоянии;
В подъемнике замка
наплавлять изношенные поверхности широкого пальца , узкого пальца , квадратного
отверстия ;
У валика подъемника
наплавлять изношенные поверхности квадрата, цилиндрические поверхности и стенки
паза болта.
Обработка наплавленных
поверхностей деталей автосцепки производится с применением фрезерных,
строгальных станков, шлифовальных машинок и специализированной оснастки.
Правку погнутых деталей
механизма осуществляют с использованием специальных штампов.
После ремонта детали и
автосцепки в сборе проверяют шаблонами и в случае соответствия ее требованиям
приемки, валик подъемника закрепляют болтом с гайкой, под головку болта и гайку
ставят фасовочные шайбы, которые загибают на головку болта и гайку.
2.6 Сборка автосцепки
СА-3
Сборка механизма автосцепки
осуществляется в такой последовательности. Подъемник укладывают широким пальцем
вверх на опору стенки корпуса со стороны большого зуба. Затем на шип этой же стенки
навешивают замкодержатель.
Далее вставляют внутрь
корпуса замок с предохранителем. При этом металлическим крючком поднимают
нижнее плечо предохранителя так, чтобы верхнее прошло над полочкой со стороны
малого зуба. Пропустив валик подъемника через отверстие в стенке корпуса,
овальный вырез замка и квадратное отверстие подъемника, фиксируют эти детали от
выпадения.
Затем вставляют запорный
болт, закрепляют механизм и соединяют цепь расцепного привода с отверстием в
балансире валика подъемника.
В правильно собранной
автосцепке:
- ударная поверхность
лапы замкодержателя и часть замка выходят в зев. При таком положении деталей
механизм готов к автоматическому сцеплению;
- замок уходит внутрь от
усилия, направленного со стороны зева или приложенного к рукоятке расцепного
рычага, и возвращается в первоначальное положение при снятии этих усилий;
- нельзя утопить замок
в корпус, если туда предварительно введена лапа замкодержателя.
2.7 Испытание после
ремонта (обмеры)
Проверка деталей
автосцепного устройства шаблонами.
После ремонта
автосцепок их детали осматривают и обмеряют шаблонами.
Шаблоны имеют установленные
номера и действуют по принципу проходных и непроходных.
Замок автосцепки:
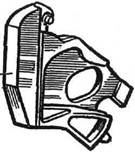
Рис. 9 Замок автосцепки.
Проверяется замок
шаблонами в соответствии с Инструкцией № ЦВ-ВНИИЖТ-494-97. При этом проверяют:
·
проходной
вырез а шаблоном 852р; Замок признают годным, если он свободно проходит через
вырез а этого шаблона.
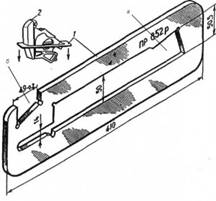
Рис. 10 Шаблон 852р.
·
толщину
замыкающей части замка по всей её высоте проверяют до ремонта непроходным
шаблоном 899р; Замок признают годным после ремонта, если замыкающая часть его
не входит вырез б шаблона 852р и негодным, если она входит в вырез б шаблона
852р (поз. 2)
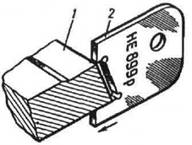
Рис. 11 Шаблон 899р
·
положение
задней кромки К овального отверстия относительно торца замка на соответствие
шаблону 839р; который накладывают на замок так, чтобы шаблон своим основанием 2
плотно прилегал к плоскости замка. Затем перемещением шаблона за рукоятку 3 в
направлении стрелки А обеспечивают плотное прилегание опорных площадок 4 к
торцевой поверхности замка, а угольника 5 – к его нижней опорной части. Удерживая
шаблон в таком положении, поворачивают за рукоятку мерительный сектор 1 по
часовой стрелке. Замок считают годным, если проходная часть мерительного
сектора 1 свободно проходит мимо кромки отверстия замка, а непроходная часть не
проходит (упирается в кромку отверстия).
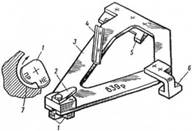
Рис. 12 Шаблон 839р
·
положение
шипа, его диаметр и кромку прилива на соответствие шаблону 833р.
При этом износ прилива шипа
по поверхности очерченной радиусом 24 мм не допускается более 3
мм.
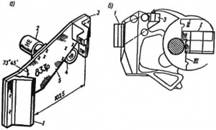
Рис. 13 Шаблон 833р
При проверке расстояния
от торцевой поверхности замка до задней боковой кромки шипа для предохранителя
шаблон надвигают на замок сверху так, чтобы опорная поверхность угольника 1,
была прижата к торцевой поверхности замка. Замок признают годным, если при
перемещении шаблона вниз проходная часть гребенки 3 проходит мимо шипа
предохранителя, а непроходная не проходит.
Диаметр шипа замка для
предохранителя проверяют непроходным и проходным стаканами этого шаблона.
Шип 1 считают годным,
если проходной стакан 2 свободно надевают на него до упора торцом в замок у
основания шипа, а непроходной стакан 3 не надевается или надевается частично
так, что торец шипа не выступает за верхнюю кромку кольца непроходного стакана.
Износ прилива для шипа
по поверхности, очерченной радиусом 24 мм, проверяется шаблоном 833р как
показано на рисунке. Зазор а более 3 мм не допускается.
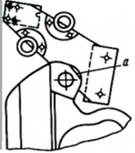
Рис. 14 Шаблон 833р.
Излом шипа не
допускается;
- направляющий зуб на
соответствие шаблону 943р, причем суммарный зазор между кромками зуба и шаблоном
не должен превышать 2 мм
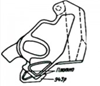
Рис. 15 Шаблон 943р.
- наличие трещин в
верхней перемычке для прохода нижнего плеча предохранителя от саморасцепа;
- наличие трещин,
погнутости и изломов сигнального отростка;
Проверяют диаметр
валика замка, который не должен быть меньше 15,5 мм, не допускаются на
нем трещины или изгибы.
При несоответствии
шаблонам или при наличии других неисправностей – замок ремонтируют.
Шаблон 821Р-1 предназначен
для проверки ширины зева (рис. 23)

Рис. 16 шаблон 821р-1.
Шаблон прикладывают
одним концом к углу малого зуба, а другой подводят к носку большого зуба. Если
шаблон входит зев, то он расширен и подлежит правке. При ТО-3 и деповском
ремонте вагонов длину малого зуба и расстояния от ударной стенки зева до
тяговой кромки большого зуба проверяют шаблоном 893Р.
Проверка выполняется в
средней части корпуса на расстоянии 80 мм вверх и вниз от продольной оси
автосцепки. Шаблон надевают на малый зуб, а также вводят в пространство между
ударной стенкой и тяговой поверхностью большого зуба. Корпус исправен, если
между ним и шаблоном имеются зазоры.
Контур зацепления
корпуса проверяют проходным шаблоном 827Р. Шаблон пропускают через контур. Корпус
исправен, если шаблон свободно проходит через него по всей высоте корпуса.

Рис. 17 шаблон 827Р.
Шаблон 852Р служит для контроля
толщины и прямолинейности замка. Замок должен пройти в проходной вырез шаблона
и не проходить после ремонта в непроходной.

Рис. 18 шаблон 852Р.
Толщину замыкающей части
замка проверяют непроходным шаблоном 899Р. замок исправен, если его замыкающая
часть не проходит в контрольный вырез шаблона.

Рис. 19 шаблон 899Р.
Исправность предохранителя
проверяют шаблоном 800Р-1, подъемника - 847Р.
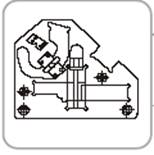
Рис. 20 шаблон 800Р-1.
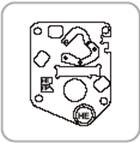
Рис. 21 шаблон 847Р.
После ремонта и
проверки шаблонами на замок, замкодержатель, предохранитель, подъемник, валик
подъемника, тяговый хомут, валик, клин тягового хомута, ударную розетку,
центрирующую балочку, маятниковые подвески, упорную плиту, корпус поглощающего
аппарата, собранную автосцепку, вкладыш и поддерживающую плиту центрирующего
прибора ставят клейма. Клейма на деталях ставят в определенных местах. Например,
на собранной автосцепке клеймо должно быть расположено на расстоянии 180 мм от
упора и на 80 мм от верха головы корпуса. Все старые клейма должны быть
зачищены. Клеймо состоит из номера ремонтного пункта и даты ремонта цифрами
высотой не менее 6 мм на глубину 0,25 мм (например, 385. 08. 00. ).
Установить на вагоны
детали автосцепного устройства без клейм не допускается.
После приемки детали
автосцепного устройства окрашивают черной краской, за исключением внутренних
поверхностей зева корпуса и поглощающего аппарата, а также деталей механизма.
При установке автосцепного
устройства на вагон необходимо проверить расстояние от упора головки корпуса до
ударной розетки, которое должно быть у грузовых вагонов с ударной розеткой,
выступающей от концевой балки на 185 мм, не менее 70 мм при полностью
утопленном положении автосцепки и не более 90 мм – при выдвинутом положении. Для
грузовых вагонов, имеющих розетку, выступающую от концевой балки на 130 мм, эти
расстояния должны быть соответственно не менее 120 мм и не более 140 мм.
2.8 Организация
рабочего места
На рабочем месте должны
находиться рабочие и контрольно- измерительные инструменты, необходимые для
выполнения заданной операции. К размещению инструментов, заготовок и материалов
на рабочем месте предъявляются определенные требования:
- на рабочем месте
должны находиться только те инструменты, материалы и заготовки, которые
необходимы для данной работы;
- инструменты и
материалы, которые рабочий использует часто, должны располагаться ближе к нему;
- инструменты и
материалы, используемые реже, должны располагаться дальше, приблизительно на
500 мм;
- досягаемость инструментов
и материалов, используемых крайне редко обеспечивается только при наклонах
корпуса работника.
Правила содержания
рабочего места.
В связи с тем, что
рациональная организация рабочего места и правильное размещение инструментов и
материалов в процессе работы играют существенную роль в обеспечении ее
качества, следует соблюдать перечисленные ниже правила.
До начала работы
необходимо:
- проверить исправность
верстака, тисков, приспособлений, индивидуального освещения и механизмов,
используемых в работе;
- ознакомиться с
инструкцией или технологической картой, чертежом и техническими требованиями к
предстоящей работе;
- отрегулировать высоту
тисков по своему росту; проверить наличие и состояние инструментов, материалов
и заготовок, используемых в работе;
- расположить на
верстаке инструменты, заготовки, материалы и приспособления, необходимые для
работы.
Во время работы
необходимо:
- иметь на верстаке
только те инструменты и приспособления, которые используются в настоящий
момент;
- возвращать
использованный инструмент на исходное место;
- постоянно
поддерживать чистоту и порядок на рабочем месте.
По окончании работы
необходимо:
- очистить инструмент
от стружки, протереть, уложить в футляры и убрать в ящики верстака;
- очистить от стружки и
грязи столешницу верстака и тиски;
- убрать с верстака
неиспользованные материалы и заготовки, а также обработанные детали;
- выключить
индивидуальное освещение.
2.9 Инструменты,
материалы, оборудование применяемые при ремонте
1. шаблон 873 –
проверка длины малого зуба.

Рис. 22 шаблон 873.
2. шаблон 940р – то же.

Рис. 23 шаблон 940р.
3. шаблон 821р-1 –
ширина зева.

Рис. 24 шаблон 821р-1.
4. шаблон 893р –
проверяется длина малого зуба и расстояние от ударной стенки зева до тяговой
поверхности большого зуба.

Рис. 25 шаблон 893р.
5. шаблон 827р – для
контроля контура зацепления.

Рис. 26 шаблон 827р.
6. шаблон 852р –
толщина замка.

Рис. 27 шаблон 852р.
7. шаблон 899р –
толщина замыкающей части замка.

Рис. 28 шаблон 899р.
8. шаблон 920р-1 –
длина хомута и проем в головной части.

Рис. 29 Шаблон 920р-1.
9. шаблон 800р-1 –
проверка предохранителя.

Рис. 30 шаблон 800р-1.
10. шаблон 847р –
проверка подъемника замка.

Рис. 31 шаблон 847р.
11. шаблон 848р – для
контроля ширины кармана для замка.

Рис. 32 шаблон 848р.
12. шаблон 914р/2М –
для контроля ударной поверхности малого зуба.

Рис. 33 шаблон 914р/2М.
13. шаблон 914р/25 –для
контроля контура зацепления.

Рис. 34 шаблон 914р/25.
14. шаблон 884р – для
контроля длины малого зуба и расстояния от ударной стенки зева до тяговой
поверхности большого зуба.

Рис. 35 шаблон 884Р.
15. Приспособление ИН
142 - для контроля длины хвостовика автосцепки.
16. шаблон 914р/21а -
для контроля ударных поверхностей контура зацепления.

Рис. 36 шаблон 914р/21а.
17. шаблон 806р - для
контроля диаметра шипа для замкодержателя.
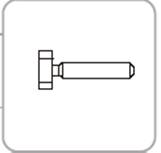
Рис. 37 шаблон 806р.
18. шаблон 797р - для контроля
диаметра соосности отверстия для валика подъемника.

Рис. 38 шаблон 797р.
19. молоток слесарный.

Рис. 39 молоток
слесарный.
20. ломик-калибр для
проверки износов в контурах зацепления автосцепок.
Страницы: 1, 2, 3, 4
|