Шпаргалка: Детали приборов
14.
Зубчатые
механизмы. Стандартизация эвольвентного зацепления. Методы нарезания колес
Эвольвентное
зацепление позволяет передавать движение с постоянным передаточным отношением. Эвольвентное
зацепление — зубчатое зацепление, в котором профили зубьев очерчены по эвольвенте окружности.
Для этого
необходимо чтобы зубья зубчатых колёс были очерчены по кривой, у которой общаянормаль,
проведённая через точку касания профилей зубьев, всегда проходит через одну и
ту же точку на линии, соединяющей центры зубчатых колёс, называемую полюсом зацепления.
В соответствии с
принципом взаимозаменяемости ряд геометрических параметров эвольвентного
зацепления стандартизован. Зубчатые колёса выбирают по числу зубьев z и модулю m,
принимая следующие параметры за постоянные (по ГОСТ 13755-81):
1.
высота
головок зуба ;
2.
глубина
впадин ;
3.
подрезания
нет, то есть x1 = x2 = 0 или угол зацепления α равен основному углу
зацепления αw;
4.
угол
зацепления α = 20 °;
5.
коэффициент
высоты головки зуба ;
6.
коэффициент
радиального зазора c * = 0.25.
Методы нарезания
зубчатых колёс
Существует два
различных метода нарезания: 1) метод копирования; 2) метод обкатки.
Цилиндрические
прямозубые и косозубые колеса нарезают дисковой или пальцевой модульной фрезой
на зубофрезерных или фрезерных станках, контурной резцовой головкой на
зубодолбежных станках, а также шлифуют профильным кругом на зубощлифовальных
станках. (рис. 1Метод непроизводителен и применяется в мелкосерийном
и единичном производстве.
Второй метод обката или
огибания может производиться с помощью инструментальной рейки (гребёнки) на
зубострогальном станке; долбяком на зубодолбёжном станке или червячной фрезой
на зубофрезерном станке. Этот метод высокопроизводителен и применяется в
массовом и крупносерийном производстве. Одним и тем же инструментом можно
нарезать колёса с различным числом зубьев. Нарезание с помощью инструментальной
рейки имитирует реечное зацепление (рис. 2, а), где профиль зуба образуется как
огибающая последовательных положений профиля инструмента, угол исходного
контура которого α=20º (рис. 2, б). Зацепление между режущим
инструментом и нарезаемым колесом называется станочным. В станочном зацеплении
начальная окружность всегда совпадает с делительной.
Самым производительным
из рассмотренных методов является зубофрезерование с помощью червячных фрез,
которые находятся в зацеплении с заготовкой по аналогии с червячной передачей
(рис. 2, в).
При нарезании долбяком
осуществляется его возвратно поступательное движение при одновременном
вращении. Фактически при этом осуществляется зацепление заготовки с инструментальным
зубчатым колесом – долбяком (рис. 2, г). Этот метод чаще всего используется при
нарезании внутренних зубчатых венцов.
Все рассмотренные
методы используются для нарезания цилиндрических колёс как с прямыми, так и с
косыми зубьями.
Конические
зубчатые колеса нарезают по методу копирования дисковыми модульным фрезами,
фасонными зубострогальными резцами и круговыми протяжками.
15.
Ременные
передачи. Виды передач. Достоинства и недостатки. Форма ремней. Напряжения в
ремнях
Ременная
передача относится к передачам трением с гибкой связью и
может применяться для передачи движения между валами, находящимися на
значительном расстоянии один от другого. Она состоит (рис.1) из двух шкивов
(ведущего, ведомого) и охватывающего их ремня. Ведущий шкив силами трения,
возникающими на поверхности контакта шкива с ремнем вследствие его натяжения,
приводит ремень в движение. Ремень в свою очередь заставляет вращаться ведомый
шкив. Таким образом, мощность передается с ведущего шкива на ведомый.
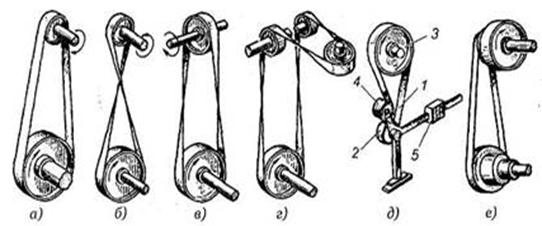
Рис.1.
Виды ременных передач: а — открытая передача; б — перекрестная передача; в —
полуперекрестная передача (со скрещивающимися валами); г — угловая передача (с
направляющим роликом); д — передача с нажимным роликом; е — передача со
ступенчатым шкивом
Классификация
ременных
передач
Форма
ремней:
-
плоскоременные (б);
-
клиноременные (в);
-
круглоременные (д);
Типы
ремней ременных передач: — плоский ремень; — клиновый ремень; — круглый ремень;
— поликлиновый ремень; — зубчатый ремень
Достоинства:
-
возможность
расположения ведущего и ведомого шкивов на больших расстояниях (более 15
метров) (что важно, например, для сельскохозяйственного машиностроения);
-
плавность хода, бесшумность работы передачи, обусловленные эластичностью ремня;
-
малая чувствительность к толчкам и ударам, а также к перегрузкам, способность
пробуксовывать;
-
возможность работы с большими угловыми скоростями;
-
предохранение механизмов от резких колебаний нагрузки вследствие упругости
ремня;
-
возможность работы при высоких оборотах;
-
простота конструкции и низкая стоимость.
Недостатки:
-
непостоянство передаточного числа вследствие проскальзывания ремней;
-
постепенное вытягивание ремней, их недолговечность;
-
необходимость постоянного ухода (установка и натяжение ремней, их перешивка и
замена при обрыве);
-
сравнительно большие габаритные размеры передачи;
-
высокие нагрузки на валы и опоры из-за натяжения ремня;
-
опасность попадания масла на ремень;
-
малая долговечность при больших скоростях (в пределах от 1000 до 5000 ч);
Клиноременная
передача.
Ременную
передачу с параллельными осями, приводной ремень которой имеет клиновую форму
поперечного сечения, называют клиноременной. Клиноременную
передачу выполняют только открытой. Клиновые ремни стандартизованы по сечению и
длине.
Клиновые ремни
применяют по несколько штук, чтобы варьировать нагрузочную способность и
несколько повысить надёжность передачи. Кроме того, один толстый ремень,
поставленный вместо нескольких тонких будет иметь гораздо большие напряжения
изгиба при огибании шкива. Клиноременные передачи в машиностроении применяют
чаще, чем плоскоременные. скорость не должна превышать 30 м/с, так как при v
>
30
м/с клиновые ремни начинают вибрировать. Оптимальная окружная скорость, при
которой передача работает устойчиво, v
=
5-25
м/с.
Различают
следующие виды напряжений в ремне.
1.
Предварительное напряжение , определяемое
в зависимости от силы начального натяжения:
σ0=F0/A
(1)
где А — площадь поперечного сечения ремня.
Для
стандартных ремней: = 1,76 МПа —
для плоских ремней; = 1,18 - 1,47
МПа — для клиновых.
2.
Удельная окружная сила (полезное напряжение) Кп. Это напряжение зависит от
передаваемой ремнем окружной силы F;.
Kn=Ft/A
(2)
Полезное
напряжений можно определить и как разность напряжений и : Кп = - (3) где и — напряжения в
ведущей и ведомой ветвях. По значению КП оценивается тяговая способность
ременной передачи.
3.
Напряжение изгиба , возникающее в
сечениях ремня при огибании шкивов (см. рис.13) и изменяющееся по пульсирующему
циклу. В плоском ремне нейтральный слой проходит посередине толщины ремня.
Наружные слои ремня при огибании шкива растягиваются, а внутренние — сжимаются.
Приближенно примем, что закон Гука справедлив и для материалов ремней, тогда
для растянутой стороны ремня , где
s =
утт/р — относительное удлинение волокон.
4.
Напряжение от центробежных сил. Это напряжение зависит от силы Fv
Fv
(5)
На
рис.13 показано, что по всей длине ремня напряжение распределяется
равномерно.
5.
Наибольшее суммарное напряжение определяется
как сумма полезного напряжения, напряжения изгиба в ведущей ветви ( и ) и напряжения
от центробежных сил ( ):
(36)
( возникает в
ремне, в месте его набегания на малый шкив (см. рис.13)).
16. Контактные
напряжения во фрикционных передачах. Передаваемый момент.
условие прочности ,
где
— допустимое контактное
напряжение для материала катков. На основании опытов допускаемые напряжения
рекомендуют принимать в этом случае при 107циклов и постоянной работе =
1000...1200 МПа.
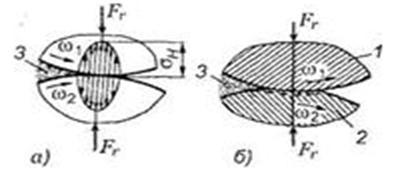
Рис.
6. Усилия и напряжения в контакте цилиндрических колес:
1—
ведущее колесо; 2 — ведомое колесо; 3 — смазочное масло
Наибольшие
контактные напряжения определяют по формуле Герца:
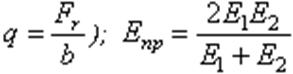

где q
—
нормальная нагрузка на единицу длины контактных линий (для цилиндрических
катков
-
приведенный
модуль упругости; Е1 и Е2 — модули упругости материалов ведущего и ведомого
катков;
-
— приведенный
радиус кривизны цилиндрических катков; R1
и
R2 — радиусы катков
(равны
-
При
перекатывании катка, имеющего радиус R,
внутри
катка (кольца) радиуса R2
приведенный
радиус кривизны (внутреннее зацепление).
Передаваемый момент
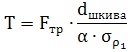
17.
Силы
во фрикционных передачах. Необходимая сила нажатия роликов. Вариаторы
Фрикционные
передачи состоят из двух катков (роликов) (рис.1): ведущего 1 и ведомого 2, которые
прижимаются один к другому силой Fr
(на
рисунке — пружиной), так что сила трения в месте
контакта катков достаточна для передаваемой окружной силы Ft.
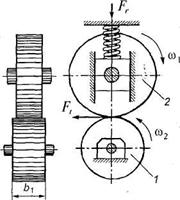
Рис.1.
Цилиндрическая фрикционная передача:
1
—
ведущий каток; 2 — ведомый каток
Условие
работоспособности передачи:
(1)
Нарушение
условия (1) приводит к буксованию и быстрому износу катков. Для того чтобы передать
заданное окружное усилие Ft.,
фрикционные катки надо прижать друг к другу усилием Fr
так,
чтобы возникающая при этом сила трения была бы
больше силы Ft.
на величину коэффициента запаса сцепления , который принимают
равным = 1,25...2,0.
Силы
в передаче.
Для
обеспечения работоспособности фрикционных передач необходимо прижать катки (см.
рис.5) силой нажатия таким
образом, чтобы соблюдалось условие (1), т. е.
(11)
где
— максимальная
сила трения; — передаваемая
окружная сила; — коэффициент
трения (выбирается по табл.1). Отсюда сила нажатия или
,
(12)
где
— коэффициент
запаса сцепления; вводится для предупреждения пробуксовки от перегрузок в
период пуска передачи (для силовых передач = 1,25
÷ 1,5; для передач приборов = 3 ÷
5).
По
схеме, показанной на рис.5,
.
(13)
Подставив
формулу (13) в формулу (12), определим силу нажатия
.
(14)
На практике применяют
два способа прижатия катков (роликов): постоянной силой и автоматическое. Постоянная
по значению прижимная сила катков допустима при передаче постоянной нагрузки.
При переменной нагрузке прижатие катков должно изменяться автоматически —
пропорционально изменению передаваемого вращающего момента. В этом случае
снижаются потери на трение, повышается долговечность передачи.
В первом случае сила
прижатия, осуществляемая обычно с помощью пружин, в процессе paботы
изменена быть не может; во втором случае сила прижатия изменяется с изменением
нагрузки, что положительно, сказывается на качественных характеристиках
передачи.
Вариаторы
— передачи, посредством которых можно плавно, бесступенчато изменять
передаточное число. По форме тел вращения вариаторы бывают лобовые, конусные,
торовые и др.
Вариатор
позволяет бесступенчато изменять передаточное отношение между двигателем и
трансмиссией. А это значит, что для каждого режима работы автомобиля (т.е.
скорости и сопротивления движению) удается подобрать наиболее эффективное
значение передаточного отношения, а не усредненное, как в любой другой коробке
передач. Главный недостаток вариаторов состоит в том, что они фрикционные
(работают за счет трения, а не зубчатого зацепления), и поэтому могут
передавать ограниченный крутящий момент, при превышении которого рабочие
поверхности начинают проскальзывать и интенсивно изнашиваться. А это означает,
что их нельзя использовать в паре с мощными двигателями.
Вариаторы
имеют КПД ниже чем простые передачи с постоянным передаточным отношением.
В
передачах с одним регулируемым шкивом (рис. 18, а) шкив подпружинен и, как
правило, насажен на вал электродвигателя, ведомый шкив постоянного диаметра —
на вал рабочей машины. Перемещением двигателя изменяется натяжение ремня,
заставляющее перемещаться диски подпружиненного шкива и изменяющее его рабочий
диаметр. В качестве тягового органа в ременных вариаторах применяют как стандартные
клиновые ремни, так и специальные широкие вариаторные ремни. Скорость
регулируют изменением диаметра одного шкивов посредством осевого перемещения
конических дисков, образующих шкив.
В
настоящее время на автомобилях применяют два типа вариатора: клиноременной и
торовый. Клиноременной состоит из двух раздвижных шкивов и натянутого между
ними ремня. Один шкив соединен с двигателем, и является ведущим, второй,
ведомый, - с ведущими колесами. Шкивы, как уже говорилось, раздвижные, то есть,
состоят из двух половинок. Если половинки шкива сближаются, ремень
выталкивается наружу, если раздвигаются, ремень проваливается внутрь. Изменение
радиусов, по которым вращается ремень, происходит синхронно - когда один шкив
увеличивает радиус, другой его уменьшает. В итоге плавно изменяется передаточное
отношение: пока радиус ведущего шкива меньше, чем ведомого, имеем пониженную
передачу; если радиусы равны - передача прямая; если же ремень на ведущем шкиве
вращается по большему радиусу, чем на ведомом — получаем повышенную передачу.
18.
Конструирование
валов и осей. Передача крутящего момента и осевой силы
Валом
называют деталь (как правило, гладкой или ступенчатой цилиндрической формы),
предназначенную для передачи крутящего момента и для поддержания установленных
на ней шкивов, зубчатых колес, звездочек, катков и т. д. Опорами служат
подшипники и подпятники
Осью
называют деталь, предназначенную только для поддержания установленных на ней
деталей. Оси обеспечивают вращающее движение звеньев, нагружены поперечными
силами и изгибающими моментами, как и валы, но не передают крутящий момент
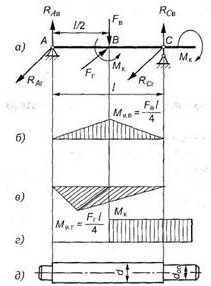 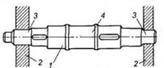
Рис.1.
Прямой вал: 1 — вал; 2 — опоры вала; 3 — цапфы; 4 — шейка
Вал 1 (рис.1)
имеет опоры 2, называемые
подшипниками. Часть вала, охватываемую опорой, называют цапфой. Концевые цапфы
именуют шипами 3, а
промежуточные — шейками 4.
Цапфой
называется участок вала или оси, которыми они соприкасаются с опорами. Цапфа,
расположенная на конце вала или оси – шип., а посередине – шейка.
Валы и
оси следует конструировать по возможности гладкими с минимальным числом
уступов. Каждая насаживаемая на вал или ось деталь должна свободно проходить до
своей посадочной поверхности. Торцы валов и осей и их уступы выполняют с
фасками (рис.3.1.2, 3.1.4) для удобства насадки деталей. Для увеличения
изгибной жесткости валов и осей насаживаемые детали располагают ближе к опорам.
Для повышения несущей способности валов и осей их поверхность подвергают
упрочнению.
В
схеме (см. рис.9, а) Мк — крутящий момент, возникающий в поперечных сечениях
вала; FB
и
FT —
силы,
действующие на вал в вертикальной и в горизонтальной плоскостях.
Страницы: 1, 2, 3, 4, 5
|