Учебное пособие: Металлы и сплавы
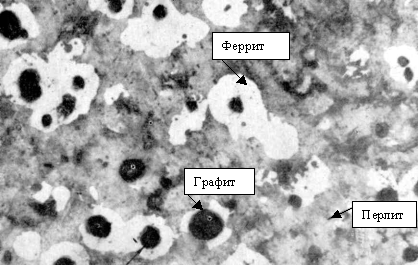
Рис. 6.5. Высокопрочный чугун с
шаровидным графитом: перлитоферритографитная микроструктура, х200
Основная структура обычно представляет собой перлит. Иногда вокруг
графита наблюдается оболочка феррита.
Высокопрочный чугун маркируется буквами: В - высокопрочный, Ч - чугун, например: ВЧ 35,
ВЧ 70. Цифра обозначает предел прочности чугуна в кгс/мм2.
Высокопрочные чугуны применяют для изготовления ответственных деталей,
испытывающих знакопеременные динамические нагрузки (коленчатые валы двигателей,
кронштейны, шестерни, тормозные диски, прокатные валки и др.).
Задание и методические рекомендации
1. Изучить диаграмму состояния «железо-цементит», на ее графическом
изображении обозначить области существования соответствующих структур и фазовый
состав сплавов.
2. Указать значения линий и точек диаграммы.
3. Дать определение и характеристику свойств основных фаз и
двухфазных структур железоуглеродистых сплавов.
4. Для заданного сплава построить кривую охлаждения и указать, какие
превращения происходят при охлаждении.
5. Изучить под микроскопом или на компьютере микроструктуру сталей
с различным содержанием углерода. Зарисовать микроструктуру. В соответствии с
диаграммой определить основные структурные составляющие и обозначить их на
рисунках. Пользуясь справочными таблицами, указать основные механические
характеристики сталей и их применение.
6. По структуре отоженной стали определить процентное содержание
углерода. Например, в доэвтектоидной стали содержится 20% перлита и,
следовательно, 80% феррита (определяем на глаз под микроскопом или по
микрофотографии). При приближенном расчете, не учитывая содержания углерода в
феррите, считают, что весь углерод находится только в перлите. В этом случае
количество углерода в стали определяется так:
100% перлита содержат 0,8% С, 20% перлита содержит х1 %
С.
Тогда х1= = 0,16%
С.
При более точном определении содержание углерода в
стали, особенно в малоуглеродистой, необходимо учитывать углерод, содержащийся
в феррите и в третичном цементите, который определяется следующим образом: 100%
феррита содержат 0,025% С (при 727°С),
80% феррита содержат х2% С. Тогда
х2= = 0,02%
С.
Содержание углерода в стали равно сумме: х1+х2.
Если сталь заэвтектоидная и ее структура содержит 95% перлита и 5%
вторичного цементита, содержание углерода в стали определяется так:
1)
100%
перлита содержат 0,8% С, 95% перлита содержат х1 % С.
Тогда х1= = 0,76
% С;
2)
100%
цементита содержат 6,67% С, 5% цементита содержат х2% С. Тогда х2= = 0,33% С.
Содержание углерода в стали равно х1+х2.
7. Рассмотреть классификацию и способы производства различных чугунов.
Изучить под микроскопом или на компьютере структуру различных марок чугунов,
зарисовать ее в таблице с обозначением основных фаз и структур. Указать
основные механические характеристики и применение различных чугунов.
Контрольные вопросы
1. Какие фазы и сложные структуры образуются в железоуглеродистых
сплавах?
2. Как называются линии, точки и отдельные области диаграммы
"железо-цементит"?
3. Как
изменяется структура сталей в равновесном состоянии по мере увеличения
содержания в ней углерода? Как классифицируются стали по структуре?
4. Как классифицируются стали по
содержанию в них углерода?
Как они
маркируются?
5. Как изменяются свойства сталей в зависимости от их структуры и
содержания углерода? Указать области применения сталей с различным содержанием
углерода.
6. Как изменяются свойства чугуна в зависимости от их структуры?
Указать области применения серых, ковких и высокопрочных чугунов.
Лабораторная работа № 7
Термическая обработка углеродистых сталей
Цель работы
1. Ознакомиться с различными видами термической обработки
углеродистых сталей и их назначением.
2. Разобраться в сущности упрочняющей термической обработки
сталей (закалка и отпуск). Научиться правильно выбирать режимы нагрева сталей
под закалку по диаграмме состояния "железо-цементит".
3. Изучить способы и технологию закалки сталей, их преимущества и
недостатки.
4. Экспериментально определить влияние на закаливаемость сталей:
а) их состава (содержания углерода); б) скорости непрерывного охлаждения из аустенитной
области.
5. Экспериментально исследовать влияние отпуска при различной температуре
на структуру и свойства закаленной стали.
6. Изучить с помощью металлографического микроскопа микроструктуру
сталей после различных видов термической обработки.
Содержание работы
Теория термической обработки сталей базируется на четырех основных
превращениях:
1) превращение перлита в аустенит при нагреве выше точек А1
или А3;
2) превращение аустенита в перлит при охлаждении ниже точек А1,
А3 (изотермический распад аустенита и распад аустенита при
непрерывном охлаждении);
3) превращение аустенита в мартенсит при закалке сталей;
4) превращения мартенсита и остаточного аустенита при нагреве
(отпуск сталей).
Для полного или частичного перевода сталей в структурно-равновесное
состояние применяют различные виды отжига.
Отжигом называют такой
вид термической обработки, при котором сталь нагревают ниже или выше
температуры критических точек, выдерживают при этой температуре и затем
медленно охлаждают.
Отжиг I рода проводят
при температурах выше или ниже температур фазовых превращений. К отжигу I рода относятся диффузионный отжиг
(гомогенизация), рекристаллизационный отжиг и отжиг для снятия внутренних
напряжений. Этот вид термообработки в зависимости от температурных условий его
выполнения устраняет химическую или структурную неоднородность, созданную
предшествующими обработками.
Отжиг II рода
заключается в нагреве стали до температур выше точек А1 или А3,
выдержке и, как правило, последующем медленном охлаждении (вместе с печью). При этом виде отжига протекают
фазовые превращения, определяющие структуру и свойства стали. Для сталей
проводят следующие виды отжига: полный отжиг с температурой нагрева доэвтектоидных
сталей выше температуры А3 и заэвтектоидных сталей выше температуры
А1 и неполный отжиг, когда температура выше А1, но ниже А3.
Структура
сталей после отжига: перлит +
феррит,
перлит или перлит + цементит. Отжиг
II рода применяют для получения
равновесной структуры в целях снижения твердости, повышения пластичности и
вязкости стали; улучшения обрабатываемости; измельчения зерна.
Нормализация (рис. 7.3, режим V4) заключается в нагреве
доэвтектоидной стали до температуры, превышающей точку А3 на 40…50°С, заэвтектоидной стали
до температуры выше критических точек Аст также на 40…50°С, в непродолжительной
выдержке для завершения фазовых превращений и охлаждении на воздухе.
Углеродистые стали после нормализации несколько прочнее, чем после отжига. Их
пластичность при этом ниже максимально возможной. Так как при производстве
полуфабрикатов (прутков, уголков, швеллеров, листов, полос и др.) методами
горячей обработки давлением после деформации их охлаждение происходит на
воздухе, то структура и свойства таких полуфабрикатов соответствуют
нормализованному состоянию, что обычно указывается в справочниках.
Настоящая работа посвящена упрочняющим видам термической обработки
углеродистых сталей - закалке и отпуску.
Закалка - это термическая операция, состоящая из нагрева стали до температуры
аустенитного состояния, выдержки при этой температуре с последующим охлаждением
со скоростью больше критической в целях получения структурно-неустойчивого
состояния. В результате закалки аустенит превращается в мартенсит.
Мартенсит представляет собой пересыщенный (неравновесный) напряженный твердый
раствор углерода в a-железе (рис. 7.1).
Уровень пересыщенности определяется содержанием в стали углерода и
характеризуется понятием «степень тетрагональности мартенсита» - с/а, где с - наибольшее ребро, а - наименьшее ребро
искаженной ОЦК кристаллической решетки мартенсита.
Таким образом, закаливаемость - способность сталей упрочняться
закалкой - зависит от содержания в стали углерода. Закаливаемыми считаются
средне- и высокоуглеродистые стали (начиная с содержания в стали 0,25% С и
более).
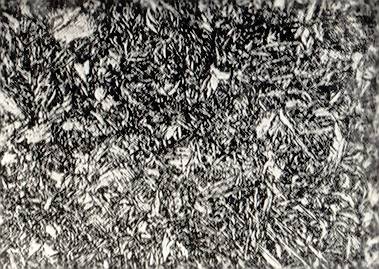
Рис. 7.1. Мелкоигольчатый
мартенсит, х500. Сталь марки У8
Определение режимов нагрева сталей под закалку
Для назначения режимов нагрева сталей под закалку используется диаграмма
«железо-цементит».
Целью нагрева является получение аустенитной структуры. При этом цементит
должен распасться, а углерод равномерно раствориться во всем объеме аустенита.
Доэвтектоидные стали нагреваются выше критических точек А3 на 30...50°С (Ас3), а
заэвтектоидные выше А1
на 30...50°С (Ас1).
Нагрев до более высоких температур вызывает рост зерна аустенита,
увеличение уровня внутренних напряжений в сталях при закалке, возможное
коробление, трещинообразование и поэтому нежелателен. Практически время
выдержки для углеродистых сталей выбирается из расчета - одна минута на каждый
миллиметр сечения детали.
Наиболее существенное влияние на свойства стали оказывает скорость
охлаждения. Изменяя скорость охлаждения, можно изменить структуру и
свойства стали. Различные закалочные среды обеспечивают следующие скорости
охлаждения в интервале температур 650...550°С: вода при температуре
18°С -
600 град/с; вода при температуре 74°С - 300 град/с; минеральное
машинное масло - 150 град/с; трансформаторное масло - 120 град/с; спокойный
воздух -
3 град/с.
Как было отмечено ранее, для превращения аустенита в мартенсит
деталь необходимо охлаждать со скоростью больше критической. При этом распад
аустенита не успевает начаться, и при температуре ниже температуры начала
мартенситного превращения (Мн) протекает бездиффузионное превращения
аустенита в мартенсит. Критическая скорость закалки – это минимальная скорость
охлаждения, при которой образуется мартенсит. Эта скорость представляет собой
касательную к линии начала распада аустенита на диаграмме его изотермического
распада. На этой же диаграмме удобно графически изобразить различные способы
закалки (координаты: температура-время, рис. 7.2).
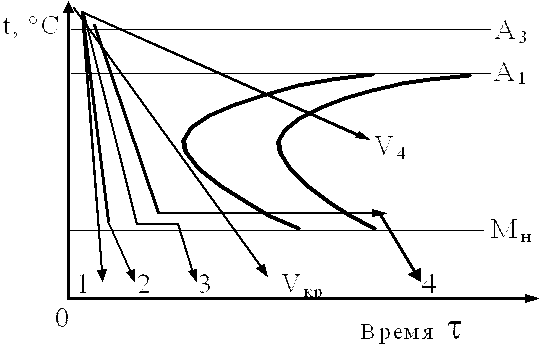
Рис. 7.2. Схема диаграммы изотермического распада аустенита для
стали У8 с нанесенными на ней режимами охлаждения при различных способах закалки
Время сквозного прогрева, максимальная температура нагрева и время
выдержки стальных деталей при нужной температуре определяются составом стали,
формой и размерами закаливаемых деталей. Способы закалки характеризуются
различными режимами охлаждения при закалке.
Непрерывная закалка (1) предусматривает охлаждение сталей в одной
среде (воде, масле или любой другой, обеспечивающей охлаждение со скоростью
больше Vкр). В результате в стали образуется мартенситная структура.
Но так как мартенситное превращение протекает быстро и сопровождается
увеличением объема, то в деталях высок уровень внутренних напряжений, возможно
трещинообразование, коробление и другие дефекты.
Прерывистая закалка (2) - это закалка в двух
средах. Сначала сталь охлаждается в среде с большей скоростью охлаждения до
температуры несколько выше Мн, а далее со значительно меньшей
скоростью. Это может быть, например,
закалка из воды в масло. Мартенситное превращение в этом случае протекает
медленнее, что приводит к снижению уровня внутренних напряжений, уменьшению
коробления и трещинообразования.
Ступенчатая закалка (3) предусматривает охлаждение с большой
скоростью до температуры несколько выше Мн , изотермическую выдержку
при этой температуре в пределах инкубационного периода (не доходя до линии начала
изотермического распада аустенита) и последующее довольно медленное охлаждение.
Этот способ практически не имеет недостатков, присущих предыдущим способам.
Перед мартенситным превращением температура детали выравнивается во всем объеме. Мартенситное превращение протекает
одновременно во всем объеме детали с умеренной скоростью.
Закалка с самоотпуском может осуществляться при закалке массивных
деталей. Охлаждение проводится по одному из вышеназванных способов до
образования в поверхностном слое мартенсита, но охлаждение деталей прекращается
в тот момент, когда внутренние слои деталей имеют еще довольно высокую
температуру и определенный запас тепла. Этого тепла должно быть достаточно для
прогрева всей детали до желаемой температуры, при которой и протекает отпуск.
Способ требует высокой квалификации термиста или регламентированной по времени
механизации процесса извлечения деталей из закалочной ванны, но не требует
затрат тепла на процесс отпуска. Закалка и отпуск выполняются с одного нагрева.
Изотермическая закалка (4) проводится так же, как и ступенчатая, но
выдержка при температуре несколько выше Мн длительная (до полного
распада аустенита с образованием бейнита нижнего (рис. 7.3)).
Изотермическая выдержка может осуществляться в расплавах солей, щелочей
или в термостатах. Этот способ закалки, как правило, не требует отпуска, а
детали со структурой нижнего бейнита имеют повышенную конструкционную прочность
и удельную ударную вязкость.
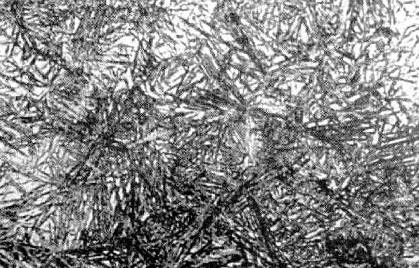
Рис. 7.3.
Бейнит нижний (игольчатый), х1000
Обработка сталей холодом. В высокоуглеродистых (С> 0,6%) и легированных сталях температура
конца мартенситного превращения ниже комнатной. При охлаждении деталей при
закалке до комнатной температуры мартенситное превращение останавливается и не
доходит до конца. В результате закалки кроме мартенсита в структуре частично
может присутствовать остаточный аустенит (Аост)(рис.7.4).
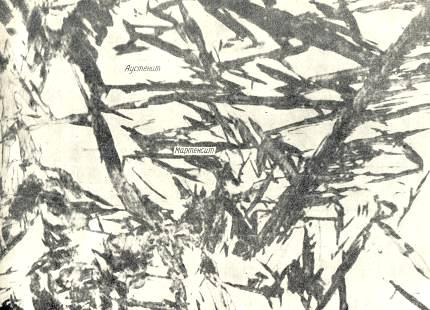
Рис. 7.4. Мартенсит и остаточный аустенит, х1000
В целях перевода аустенита в мартенсит и
завершения процесса упрочнения при закалке, а чаще для стабилизации размеров закаленных
деталей их непосредственно после закалки охлаждают в течение 3-4 часов при температуре -60...-70°С (ниже Мк). При этом остаточный аустенит
превращается в мартенсит. После обработки холодом стали чаще всего подвергают
низкому отпуску.
После закалки стали с мартенситной структурой находятся в термодинамически
неустойчивом состоянии, имеют максимальную твердость и прочность и минимальную
пластичность. Промежуточные показатели механических свойств можно получить
путем нагрева.
Термическая операция, заключающаяся в нагреве закаленных сталей до
температур не выше критических, называется отпуском сталей. На практике
различают три вида отпуска: низкий, средний и высокий.
Низкий отпуск - это нагрев закаленной стали до температур
130...250°С, выдержка и охлаждение. При этом снижаются внутренние напряжения,
мартенсит закалки превращается в мартенсит отпуска или отпущенный мартенсит
(рис. 7.5). Немного улучшается вязкость без заметного снижения твердости. Высокоуглеродистая
сталь после низкого отпуска сохраняет твердость в пределах 58...63 HRС и имеет
высокую износостойкость. Этому виду отпуска подвергают режущий инструмент,
детали после поверхностной закалки, а также после цементации и закалки.
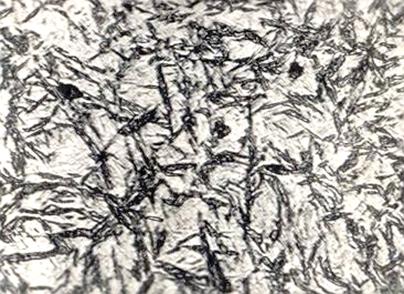
Рис. 7.5. Мартенсит
отпуска, х500. Сталь марки У8
Средний отпуск проводится путем нагрева закаленных деталей до температур
350...500°С. Структура стали после отпуска - троостит отпуска (феррит
и коагулированные частицы цементита) (рис 7.6).
Твердость средне- и высокоуглеродистых сталей - в пределах 40...50 НRС. Стали при этом имеют высокий предел
упругости, предел выносливости и релаксационную стойкость. Средний отпуск
применяют обычно для пружин, рессор и большинства ответственных сильно
нагруженных деталей авиационной техники.
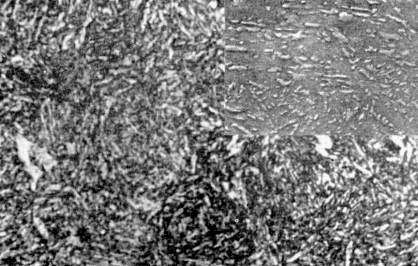
Рис. 7.6.
Троостит отпуска, х1000 (справа вверху – то же, х15000)
Высокий
отпуск проводится при температурах 500...680°С. При этом образуется структура - сорбит отпуска (феррит и цементит
зернистого строения) (рис. 7.7), обеспечивающая стали наилучшее соотношение прочности
и вязкости.
Высокий отпуск применяют для тяжелонагруженных деталей, испытывающих
ударные нагрузки.
Термическую обработку, состоящую из закалки и высокого отпуска, называют
улучшением сталей.
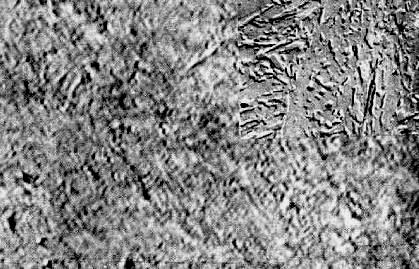
Рис. 7.7. Сорбит
отпуска, х1000 (справа вверху – то же, х15000)
Длительность нагрева при отпуске - 1-2 часа и более. Во
избежание термических напряжений после отпуска рекомендуется медленное охлаждение,
за исключением сталей, подверженных обратимой отпускной хрупкости, которые от
температуры высокого отпуска охлаждают в воде или масле.
Задание и методические рекомендации
1. Изучить содержание работы и заполнить вводную часть отчета по
предложенной форме.
2. Нарисовать часть диаграммы «железо-цементит» (область
сталей), указать на ней область закалочных температур. Выбрать температуру нагрева
под закалку сталей 30, 45, У8.
3. Нарисовать диаграмму изотермического распада аустенита и нанести на ней кривые охлаждения для
нормализации и различных способов закалки: а) непрерывной; б) прерывистой в
двух средах; в) ступенчатой; г) изотермической.
4. Выполнить закалку в воде углеродистых сталей марок 30 , 45, У8.
Измерить твердость и построить график зависимости твердости закаленной стали от
содержания углерода. Указать причину изменения твердости.
5. Нагреть до закалочной температуры и провести охлаждение стали
45 или У8 в различных охлаждающих средах (воздухе, масле, воде); измерить
твердость образцов, пользуясь данными таблицы, построить график зависимости
твердости от скорости охлаждения. Указать причину изменения твердости.
6. Провести закалку образцов из стали 45 или У8 в воде и отпуск
при различных температурах (температуры отпуска указаны в соответствующей
таблице журнала-отчета). Измерить твердость образцов после отпуска и построить
график зависимости твердости стали от температуры отпуска. Объяснить причину
изменения твердости. Указать структуры, образующиеся при различных температурах
отпуска.
7. С помощью металлографического микроскопа или компьютера изучить
микроструктуру сталей (4-5 микрошлифов) после различных видов термообработки.
Сделать зарисовку микроструктур. Указать свойства и применение сталей после
соответствующих видов термической обработки.
Контрольные вопросы
1. Как выбирают температуры нагрева под закалку для доэвтектоидных
и заэвтектоидных сталей?
2. Какие структуры получают при изотермическом распаде аустенита?
3. Что такое критическая скорость закалки? Что представляет собой структура
сталей после закалки?
4. Какие существуют способы закалки в зависимости от режима охлаждения?
В чем их отличие?
5. Охарактеризуйте виды отпуска в зависимости от температуры. Каковы
структура, свойства и применение сталей после различных видов отпуска?
6. В
каких случаях в стали после закалки кроме мартенсита присутствует остаточный
аустенит? Как его перевести в мартенсит?
Лабораторная работа № 8
Страницы: 1, 2, 3, 4, 5, 6, 7, 8, 9, 10, 11, 12, 13, 14, 15, 16
|